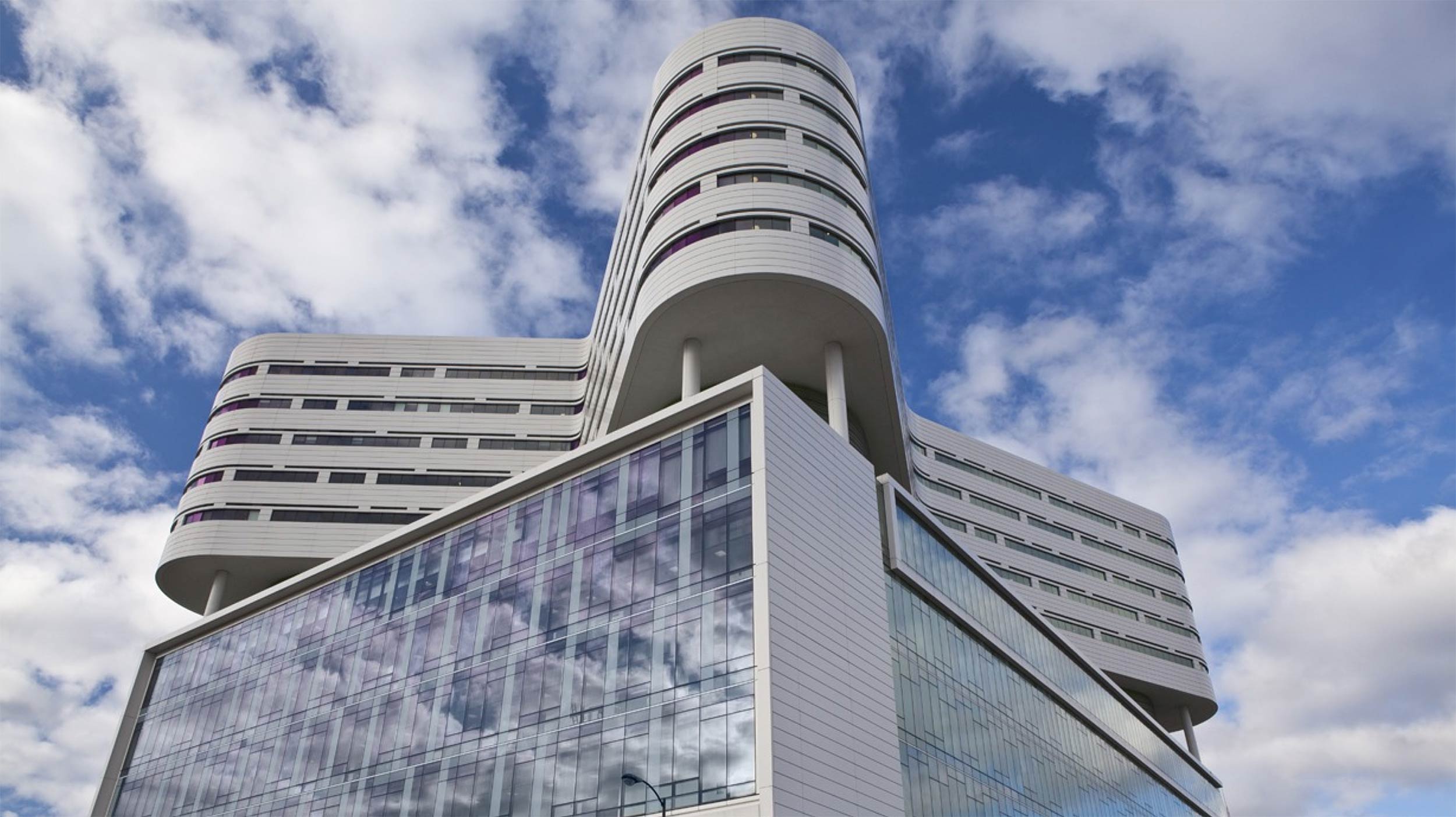
Founded in 1837, Rush University Medical Center (RUMC) is now Chicago’s second-largest hospital with multi-story buildings that dominate the city’s medical district.
The challenge
But that prestigious location posed problems when RUMC’s 11-story Professional Building 2 needed to replace two aging centrifugal chillers. It appeared the only alternative was to move a crane down a crowded street to lower new chillers through the roof. But some simple surgery made it possible for Smardt split-shell chillers with Danfoss Turbocor® compressors to simply take an elevator up to the penthouse mechanical room, a solution that cut installation costs while boosting energy savings.
“The professional building was using two fixed-speed 300-ton water-cooled centrifugal chillers,” says Mike Scalleta, mechanical systems manager at RUMC. “They were installed when the building was built in the 1970s. Consequently, the old centrifugal chillers were using twice the energy compared to today’s more efficient variable-speed chillers. It was time for them to go. The problem was we’d have to cut open the mechanical room and use a crane to drop in conventional replacement chillers.
The solution
Fortunately, we learned Smardt had a solution. Their split-shell Smardt chiller design with compact Danfoss Turbocor centrifugal compressors could be taken apart to fit into our freight elevator. Using the elevator would minimize building disruption and reduce installation costs and the efficiency of a variable-speed Smardt chiller would dramatically cut our energy costs.”
The energy efficiency of the Smardt chiller turned out to be a big plus that fit into a small space.
According to Bullock, Logan and Associates’ Curt Bullock, Jr., a Chicago representative for Smardt, the difference between the Smardt chiller and the old centrifugal chiller was night and day. When the old chiller was new, its integrated part-load value (IPLV) was 0.716 kW/ton but used oil-lubricated bearings. Because oil fouls heat exchanger tubes over time, actual efficiency was worse. “In comparison, the IPLV of the Smardt chiller is 0.315 kW/ton —
57 percent more efficient,” Bullock says. ”That’s partly because there are no oil-related heat transfer losses and no mechanical bearing friction losses. Another energy-saving feature is the compressor’s ability to adjust automatically to off-design conditions. The Danfoss Turbocor TT400 compressor can turn down capacity to 10 percent of its total capacity. By automatically matching capacity to the load, the compressor reduces its speed, which also reduces energy consumption.”
But all that efficiency wouldn’t do any good if the chiller didn’t fit into the mechanical room. “Professional Building 2 is sandwiched between Harrison Street, other professional buildings and rail lines in the Medical District,” says Carl Wigginton, vice president of service for Murphy & Miller, Inc., the Chicago-based HVAC contracting firm who handled the installation. “There is no easy access. It’s a big reach — the crane would have to come in about 100 feet, then travel another 100 feet to the mechanical room doorway. But, there is a freight elevator that goes right to the penthouse mechanical room. It’s so much easier that way — if a chiller can fit into the elevator.” The empty weight of a 300-ton WA0962HG4 Smardt chiller is about 8,500 pounds — and designed to be taken apart and easily reassembled. . Disassembly took about half a day. We transported the parts by elevator to the penthouse. “The building’s large freight elevator was rated to hold up to 7,000 pounds. A conventional 300-ton centrifugal chiller would weigh around 12,000 pounds empty. Consequently, the weight and size dimensions prohibit using the elevator.
Reducing Centrifugal Compressor Complexity with Oil-Free Magnetic Bearings.
The installation was also simplified because Danfoss Turbocor compressors don’t require an oil management system.
“In a hermetic compressor, oil circulates within the refrigerant gas. To maintain oil at proper levels, the oil management system uses elaborate piping, traps and risers. But Smardt chillers avoid all that complexity. Because the Danfoss Turbocor centrifugal shaft levitates within a magnetic field, the need for oil is eliminated.”
“Danfoss Turbocor magnetic bearings use a digital controller that processes signals from 10 sensor coils,” says Rob Silecchia, director of healthcare and pharma applications at Smardt Chiller Group. “Shaft movements of less than 0.00002-inch are detected and the magnetic field is adjusted to maintain the shaft orbit. Backup 9 / 9 AC316960753058 © Danfoss | DCS (LMT) | 2019.09 carbon or roller bearings are used only to hold the shaft when the compressor powers down.” The Danfoss Turbocor compressor’s digital intelligence also incorporates a powerful but user-friendly control system that interfaces with the Smardt chiller controller. The full-color control interface simplifies system configuration and commissioning through the chiller controller.
Another benefit is the Smardt chiller’s quietness. “With a Smardt chiller, the magnetic bearings position the shaft so precisely, there’s hardly any noise or vibration. The chiller does not have vibration-damping springs or sound-attenuating blankets. In fact, when we first visited the mechanical room to see the Smardt chiller in operation, we weren’t sure it was running — it’s that quiet compared to our old fixed-speed centrifugal chiller.”
The calculated difference in efficiency meant that over the eight-month cooling season, the new chiller saved about $12,000 more in utility costs than the proposed replacement chiller. In comparison with the old chiller, however, the new Smardt chiller saved approximately $75,000.00 in annual operating costs. When you add in the installation savings, the cost difference between the split-shell Smardt chiller and the competing chiller paid for itself in the first year of operation.
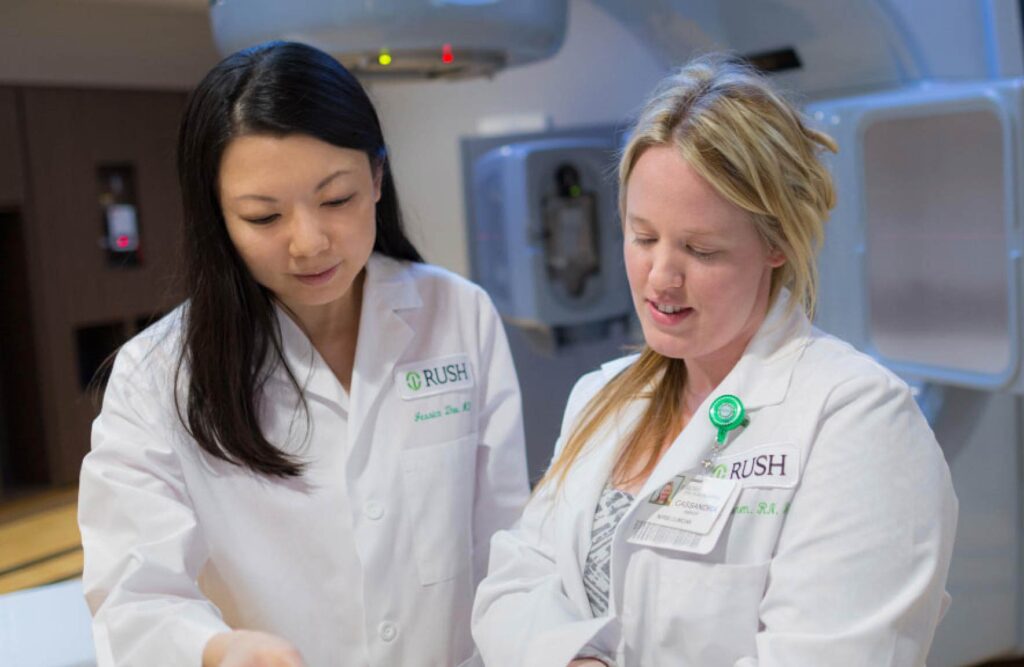
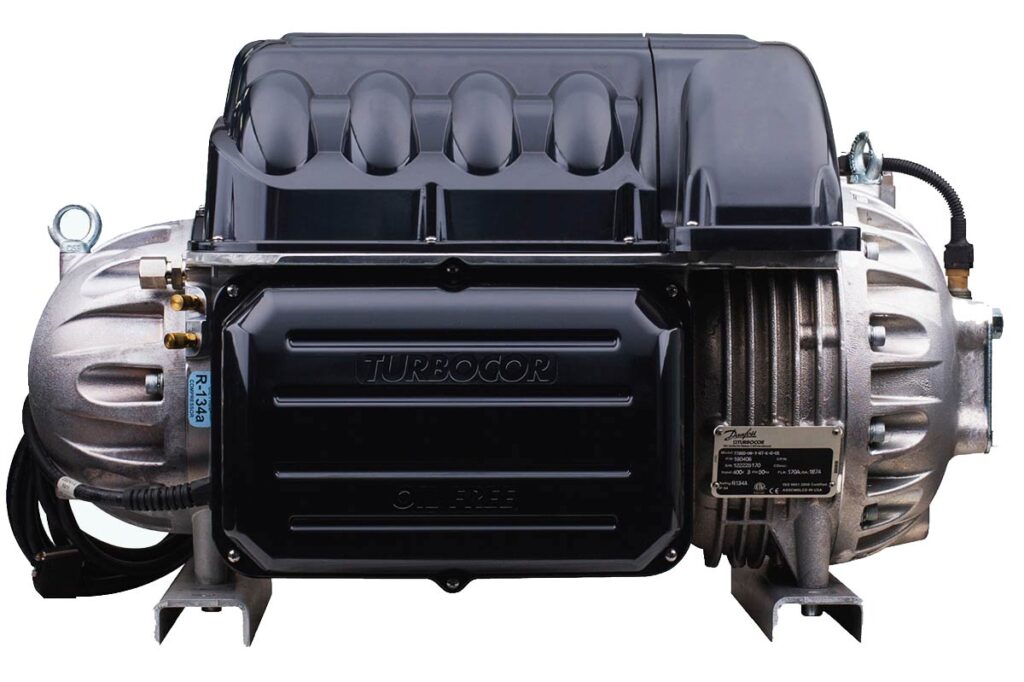
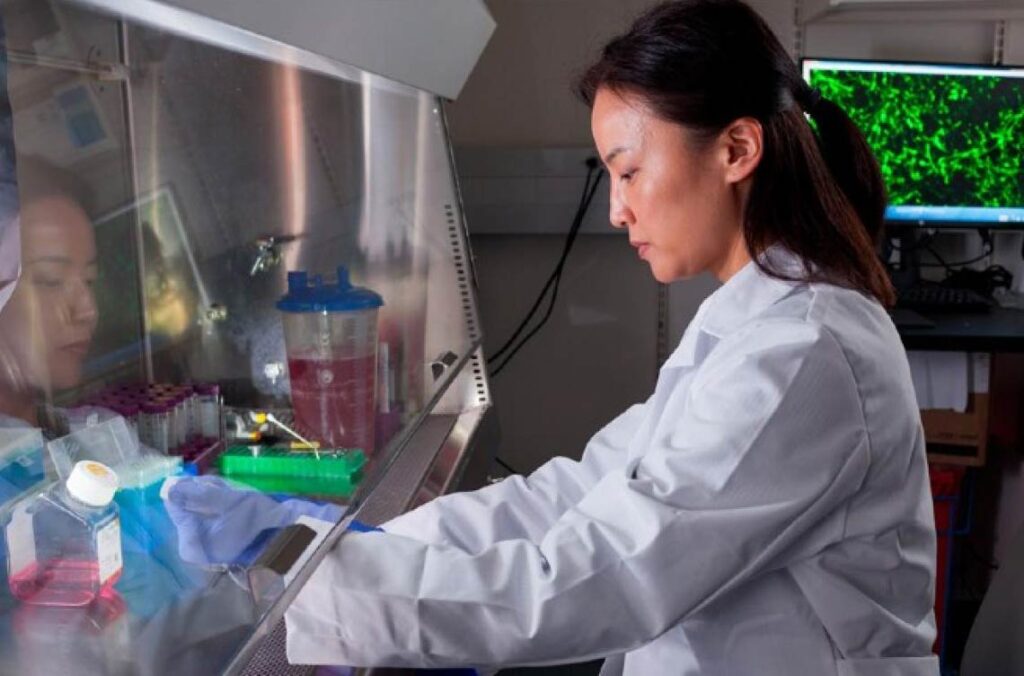
Conclusion
Combining the installation, efficiency, and acoustic advantages, it was not a difficult decision when RUMC accelerated the replacement of its second old centrifugal chiller with another split-shell Smardt chiller just three months after the first was installed. “The Smardt chiller runs smoothly and quietly,” Scalleta says.“That’s important to us and so are the energy and maintenance benefits. All the problems with oil are a thing of the past, because there is no oil.
There’s very little maintenance with these units. Smardt and Danfoss have created a clean, compact chiller design that fits perfectly into our operation.